The injection mold is the premise of plastic moulding service, which gives the shape and size to the plastics in the injection processing, although the mould structure may vary greatly due to the variety and performance of plastics, the shape and structure of plastics products and the type of injection machine, the basic structure is the same.
Plastic injection mould commonly consists of two main parts: a hollow block with cavity (forming the shape) and the moveable side for controlling the mold opening and closing.
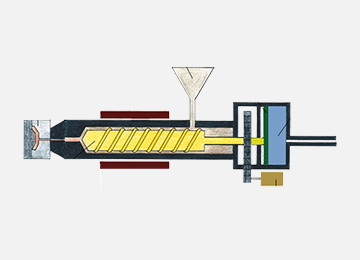
Mold design is the key factor to determine the quality of finished products. Strength, durability, shape and size depend on the type of plastic injection mold used. The cavity with runner need to be designed based on drawings or products structure, dimensions, materials performance, and requirements, go through cooling, drilling screw holes, CNC machining, polishing, fitting, assembly and more.
Plastic injection molding services is a widely applied manufacturing method for mass production needs of finished plastic parts, which using the injection molding machine, with the molten material forced into the required mold and obtain the final plastic products in mould shape. The flow plastic would cool and harden in the mold cavity and form the final shape, then the product will be ejected. The plastic injection moulding services generally avoid the secondary processing and make lots of profits. A host of complex plastic injection molds takes critical part in the process.
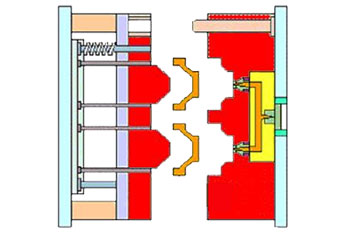
Whether the injection molding services can get a better profit, the cycle is a crucial factor. Injection molding cycle refers to the time required to complete a single injection moulding process when the mould is continuously manufactured. It consists of injection, holding, cooling and auxiliary. Injection time refers to the time when the plunger or screw moves forward the plastic melt during the flow filling. Pressure holding time refers to the time when the plunger or screw stays in the forward position to maintain pressure. Cooling time refers to the period from the end of holding pressure to the opening of the die, which is used to cool the plastic parts in the cavity. Auxiliary time refers to the time required for opening, cleaning, spraying release agent, inserting, opening, removing and closing the mould. The brief injection molding cycle can be concluded as below:
- Close the two halves of the plastic injection mold with a clamping unit and attach with the moulding machine.
- Inject the plastic material to the machine and move towards the mold.
- The plastic inside mold start to cool and when it hardens, the desired shape is completed.
- The plastic part push out by an ejection system when the mold opening.
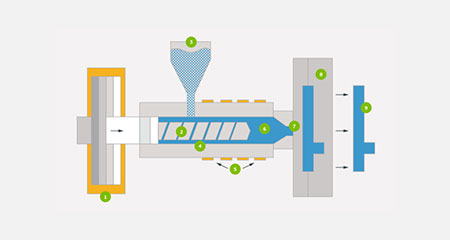
- Large volume production available
- Save cost and time as much as possible
- Reduce the manual operation and errors
- Exact molded parts with high accuracy and precision
- Minimize the material waste
- Excellent repeatability and flexibility
- Without second machining
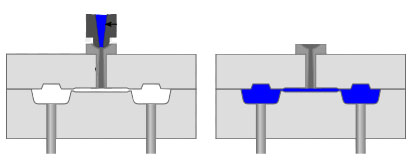
Plastic Injection Mould Co., Ltd is a China professional plastic mold design and injection mould making company with over 13 years experience. With the sophisticated technical team, we are specialized in a variety of plastic injection moluding services. PIM performs best at insert molding, unscrewing mold, 2-shot molding and stack mold. We operate advanced production equipment and facility, 24/7 climate control and process monitor in the workshop to protect the lifespan of your tool. Since its inception, our mission has been to build qualified molds with high cost performance ratio and fast turnaround delivery time, which lives on today and sets us apart from others. To know about more about our plastic injection moulding services and mold design, contact us right now.
Injection Molding Services Capabilities: We are good at making various complex mold constructions, which include insert molding, stack mold construction, two-component construction, helical gear structure, unscrewing structure, secondary slider structure, and hydraulic core pull. We also have rich experience in hot runner technology, gas-assisted injection molding, and mold flow analysis.
Product concept design
RP making (CNC for prototyping)
Product design analysis
Mold designing
In-house mold manufacturing
Part inspection report
Detailed list of mold components and spare parts Mass injection molding
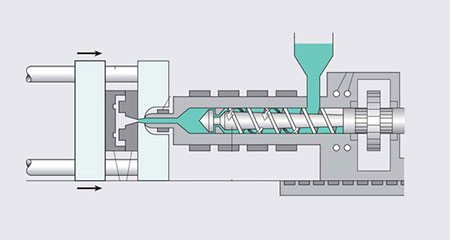
PLA injection molding, ABS injection molding, Nylon injection molding, PVC injection molding, Polycarbonate injection molding
Our clients from automotive, household appliance, electronics, communications and more industries, car molding, medical molding, and bumper molding would be a key part.
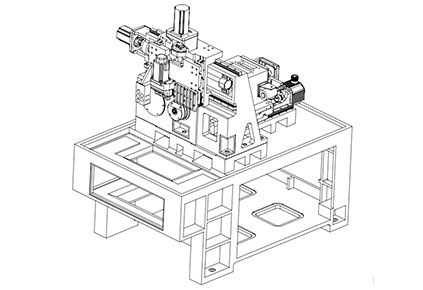
- Services
- Materials
- Industries